Choosing between refitting an existing yacht and starting a new build depends on your goals, timeline, and how far you want to personalize your vessel. A well-executed refit can breathe new life into a proven hull, giving owners the chance to update systems, interiors, and layout without starting from scratch. For some clients, a refit offers a faster turnaround and a more cost-effective path—especially if the boat’s structural integrity is solid and its bones fit the intended purpose. But refits also come with unknowns: hidden corrosion, outdated wiring, or incompatible systems can all add complexity to the project.
A new build, on the other hand, gives you complete control. Every element—from hull type to interior layout to propulsion—is designed around your cruising plans, lifestyle needs, and long-term vision. You avoid the compromises that come with working within the limits of an older design and gain the benefit of building with modern materials, more efficient systems, and full compliance with the latest safety standards. In many cases, the decision comes down to whether you want to adapt something to your needs or build something that’s tailored from the start. We help our clients navigate this decision by asking the right questions early and guiding them toward the most rewarding ownership experience.
Understanding the Difference Between Yacht Refit and New Construction
Defining a Yacht Refit Project
A yacht refit typically involves upgrading or replacing major systems, refreshing interior elements, or making structural modifications to an existing hull. Full refits often include overhauls of electrical, mechanical, and plumbing systems, as well as interior redesigns and exterior repainting. Partial refits may focus on soft goods, electronics, or targeted engine work. The scope can range from a light refresh to near-total reconstruction, depending on vessel condition and owner goals.
When we evaluate a refit, we look at three main areas: systems, structure, and aesthetics. Refits offer potential cost savings, especially if the hull and main structure are in good shape. However, they can introduce unexpected complexity. Older boats may hide corrosion, outdated materials, or obsolete hardware. These unknowns can extend timelines and increase budget uncertainty—something we factor in carefully before any refit is approved to move forward.
What Constitutes a New Yacht Build
A new build starts from the keel up, allowing complete freedom in how the yacht is designed, engineered, and outfitted. With no constraints from an existing platform, we can tailor every element—from hull geometry to cabin layout—to a client’s specific cruising goals. This approach also gives us the flexibility to use the latest in propulsion technology, power systems, insulation, and lightweight composites, while ensuring the vessel is built to current standards from day one.
Clients who opt for new construction benefit from better long-term serviceability and a lower risk of hidden problems. We’re able to build access points into bulkheads, route wiring through structured chases, and allocate space for future upgrades. That kind of planning is difficult—if not impossible—to retrofit into an older yacht.
Primary Motivations Behind Each Option
Many clients pursue a refit because they already own the boat or have found a hull with sentimental value or a proven reputation. Refits can also be attractive for buyers seeking faster delivery and lower up-front costs. In some cases, it’s simply about wanting to personalize a yacht that’s already in hand.
On the other hand, clients choose new builds when they want to define every detail of the yacht to match their lifestyle. New builds make it easier to integrate cutting-edge systems, maximize fuel efficiency, and eliminate the compromises inherent in legacy layouts. Market availability also plays a role. If there’s a lack of suitable pre-owned vessels or if timelines permit, many clients find greater satisfaction in building from scratch—even if it takes longer to deliver.
Budget Planning, Ownership Costs, and Timeline Factors
Comparing Total Investment Requirements
Refits often present a lower initial outlay than new construction, but they can come with more financial unpredictability. Labor costs can increase when old systems don’t match new components, or when underlying issues—like delamination, hidden rust, or rotted wood—are uncovered during demolition. With a new build, costs are staged and controlled throughout the project, allowing more clarity in budgeting over time.
Parts compatibility is another factor. Retrofitting components onto legacy platforms often requires custom fabrication or adaptation, which adds time and labor. In contrast, new builds benefit from cohesive system integration that’s planned from day one, which usually results in better long-term cost efficiency.
Lifecycle and Long-Term Ownership Costs
New yachts typically offer lower maintenance costs in the first 5–10 years of ownership, thanks to more efficient systems, modern materials, and better access. Refit yachts, while improved, still operate within the constraints of older infrastructure. That can mean more frequent service intervals, higher insurance premiums, and closer scrutiny during surveys.
When considering return on investment, resale value is also part of the equation. A new yacht holds its value longer, especially when backed by documentation and warranty support. A refitted vessel may increase in value over its pre-refit condition, but buyers tend to discount refits unless the work was extensive and professionally documented.
Project Duration and Scheduling Factors
Refits can be quicker to start—especially if the yacht is already in a service yard—but the timeline depends heavily on project scope and discoveries along the way. Replacing a generator or repainting topsides may take weeks, but structural or interior redesigns often stretch into months, particularly if parts are delayed or repairs uncover deeper issues.
New builds require more lead time before hull construction begins but often run on a more predictable schedule once underway. Delays are more likely to result from material sourcing or design changes rather than the unknowns that accompany teardown and inspection of older vessels. For clients working on tight cruising schedules, this predictability can make a big difference.
Technical Flexibility and Customization Potential
Structural and Layout Limitations in Refits
Refits work within the boundaries of an existing hull, which means structural bulkheads, tankage, and stringers can limit how much interior layout can be changed. Moving heads, reconfiguring cabins, or enlarging galley spaces may require significant modifications and must be reviewed for structural compliance and safety.
Older structures also raise questions around load distribution and trim. When layouts shift, so does weight balance—requiring recalculation of center of gravity, tank placement, and even stabilizer position. While it’s possible to modify these elements, the cost and complexity often increase exponentially.
Unlimited Possibilities with New Construction
With a new build, the layout is defined by your vision—not by what already exists. That allows us to build around your daily usage patterns—whether you need a quiet workspace, expanded galley, larger utility room, or full-beam master suite. We can design technical areas for long-range autonomy, including dedicated battery banks, solar controllers, engine access, and additional tankage.
It’s also easier to design with future upgrades in mind. We include wiring chases, dedicated compartments for stabilizer installs, and panel space for solar inverters or lithium expansion. Planning for the long-term starts with smart design choices, and a new build offers that freedom.
Customization Depth: Refit vs. New Build
Some systems lend themselves well to refits—like lighting, electronics, and furniture. These upgrades can dramatically improve usability and aesthetic appeal without altering the yacht’s fundamental systems. But when changes extend to the engine room, tankage, or structure, the cost can rival that of a new build.
At a certain point, a refit becomes a rebuild—and many clients begin to question whether starting fresh would have made more sense. We help our clients recognize that tipping point early, so they don’t end up overinvesting in a platform that still doesn’t meet their full expectations.
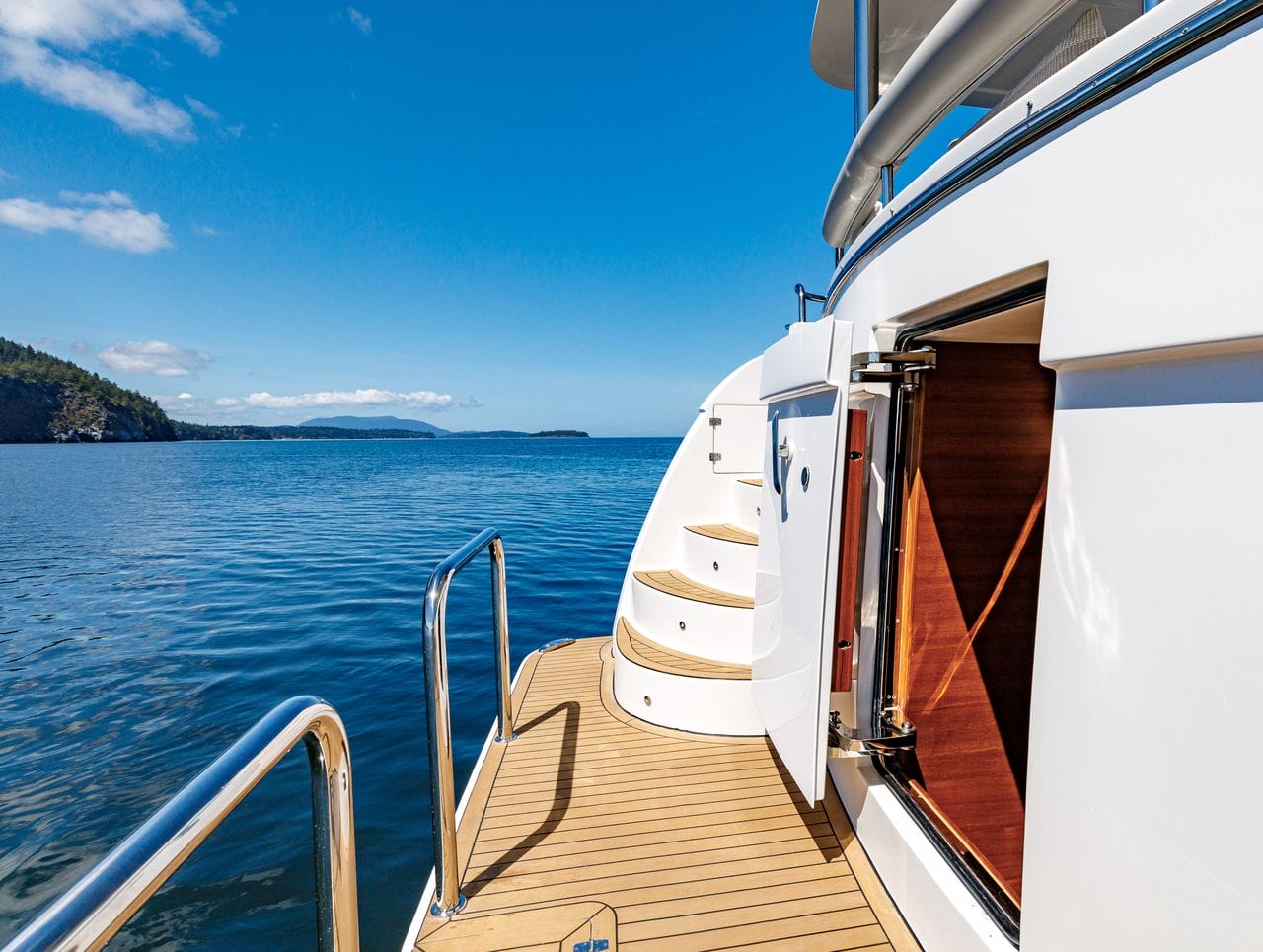
Technical Upgrades, Interior Fit-Out, and Long-Term Planning: Choosing Between Refit and New Build
Replacing or Upgrading Existing Systems
Modernizing the mechanical systems in an existing yacht often starts with engine repower—one of the most complex upgrades in a refit. Swapping out older engines for newer, more efficient models can improve performance and reduce fuel burn, but mounting geometry, shaft alignment, and exhaust routing must all be recalculated. Generator replacements and HVAC system upgrades come with their own challenges, especially when trying to retrofit equipment into tight or outdated compartments.
Rewiring is often more intensive than anticipated. While replacing light fixtures or adding electronics is straightforward, fully upgrading a yacht’s electrical system may require new breaker panels, routing paths, and grounding plans. In many refits, it becomes a balance between preserving original systems and replacing enough components to meet modern safety and efficiency standards without rebuilding the entire infrastructure.
New Build Mechanical Integration Advantages
When we build from scratch, we’re able to engineer systems for ideal balance, access, and reliability. That means designing engine rooms with full walk-around access, properly isolating generators, and routing plumbing and ductwork in a way that minimizes noise and maintenance disruption. It also allows us to center-load weight for trim, factor in redundancy, and ensure all equipment is accessible without dismantling furniture or flooring.
A clean-sheet mechanical plan means we can integrate fuel management, battery banks, HVAC zoning, watermakers, and waste systems from the outset. Systems are laid out logically, with labeled manifolds and service points grouped for efficiency. And because we build with long-range cruising in mind, we design for autonomy: backup pumps, cross-feeds, bypass loops, and pre-installed conduits for future expansion.
Safety and Compliance Considerations
One of the most important aspects of a modern refit is compliance. If systems are significantly altered, older yachts may need to meet newer standards like ABYC, CE, ISO, or MCA—especially for insurance or resale. That means applying fire-rated materials, revalidating floatation tests, or re-certifying electrical and fuel installations. These requirements often increase both timeline and budget, particularly when working with older construction methods or layouts.
New builds, by contrast, are held to modern safety standards by default. Everything we install—from structural insulation to electrical panels—is selected and installed to meet or exceed today’s marine safety codes. The result is less regulatory risk, easier certification, and smoother survey processes.
Interior Fit-Out and Customization Potential
Design Constraints in Legacy Vessels
Aesthetically, older yachts can be beautiful—but modifying them comes with limits. Matching wood tones, bulkhead spacing, or floor elevations isn’t always possible, and there are often hidden structural elements that restrict major layout changes. Removing cabinetry or walls may require additional support framing, while updating finishes may uncover water intrusion or mold that needs remediation.
Galley and head reconfigurations are particularly sensitive. Moving plumbing, raising sole levels, or rerouting HVAC ducting often snowballs into larger construction projects. While many of these changes can be made, they typically require more labor hours and engineering review than expected.
Full Design Freedom in New Interiors
With a new build, clients can select every detail of the interior from the outset. That includes layout, finishes, lighting, and even acoustic behavior. Whether we’re designing a yacht for full-time liveaboard use, remote work, or luxury charter, every cabinet, lighting circuit, and furniture piece is built with intention—not adaptation.
We can incorporate built-in furniture, optimize headroom, and ensure quiet HVAC flow with concealed ducting and vibration isolation. Clients often appreciate the ability to define how they’ll live aboard—not just how the space looks, but how it functions when under way, at anchor, or in port for months at a time.
Refitting Interior Spaces to Modern Standards
Refitting interiors can still deliver exceptional results when done strategically. Upgrades like LED lighting, soft-close cabinetry, new upholstery, and improved galley appliances can transform usability and comfort. We often install insulation, add soundproofing layers, or improve air circulation to create a fresher, more comfortable interior environment.
However, it’s important to know when a refresh isn’t enough. If structural flooring is compromised or mold has taken hold in multiple zones, a full gut and rebuild may be the smarter route. We guide clients through these decisions by assessing interior condition and weighing the cost-benefit of renovation versus replacement.
Resale Outlook and Long-Term Ownership Goals
Market Appeal of a Refit vs. a New Custom Build
Well-documented refits can enhance resale value—especially when the work modernizes key systems and improves onboard comfort. However, buyers often view refitted yachts with some skepticism unless the scope was extensive and professionally managed. New builds tend to attract stronger offers and maintain value longer, largely because their history is known and the systems are modern from the start.
Refit yachts may appeal to niche buyers who appreciate legacy brands or specific hull designs, while new builds generally reach a wider pool of potential owners, particularly in the charter or long-range cruising segments.
Future-Proofing and Upgrade Potential
Older hulls have limits. Structural fatigue, outdated hull forms, or limited load capacity may cap future potential. Even with thorough upgrades, some legacy designs simply weren’t built for today’s tech or cruising expectations. That said, many classic hulls still offer a solid platform for modernization if the underlying structure is sound.
New builds give us the opportunity to design for future adaptation. That means leaving space for lithium upgrades, solar expansion, or propulsion changes down the line. We install conduits, use scalable distribution panels, and keep all major systems accessible so that evolving technologies can be integrated years down the road without major structural impact.
Emotional and Strategic Factors
Sometimes the decision isn’t just technical—it’s personal. Clients may want to keep a family yacht in service, transform a legacy vessel with sentimental value, or preserve a well-known hull from a respected builder. Those projects are meaningful, and we approach them with respect and care.
Others are looking to make a strategic lifestyle move—investing in a new yacht designed to carry them through retirement, full-time cruising, or even global travel. In these cases, building new often offers peace of mind, better control, and the satisfaction of knowing every detail was chosen with intention.
Making the Right Decision for Your Needs
Questions We Ask Every Client
The first step is always a conversation. We ask where you plan to cruise in the next 5–10 years, how long you plan to stay aboard, and whether you prefer to customize an existing platform or shape a new one from scratch. We also talk about timeline, involvement, and what ownership looks like to you—because every decision we make comes back to how you want to use your yacht.
When a Refit Makes the Most Sense
A refit is often the right choice when the hull is proven, the systems need moderate updating, and the desired upgrades fall within the vessel’s structural and layout capabilities. It can also be the better option when timeline and budget are primary drivers, and when sentimental value is a key factor.
When a New Build Is the Better Fit
A new build is ideal for those who want full control—of layout, design, systems, and performance. If you’re planning to live aboard, cruise full time, or integrate advanced technologies, building new allows us to engineer every element around those goals. For clients focused on long-term ownership, adaptability, and modern standards, a new build offers unmatched value over time.
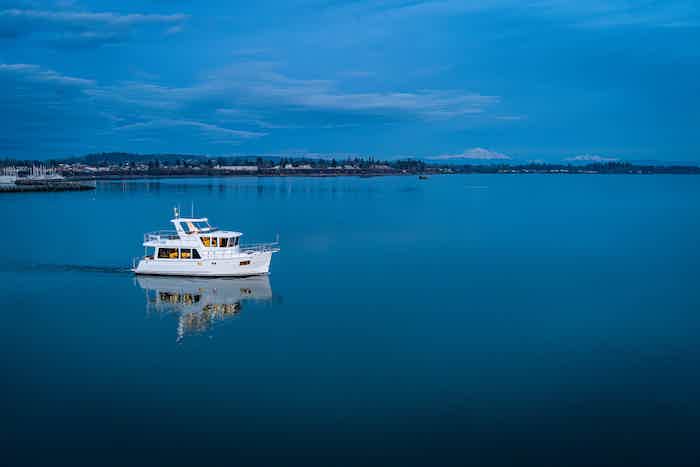
Contact Us
At North Pacific Yachts, we’re here to make your journey to owning the perfect yacht seamless and enjoyable. Whether you’re looking for expert guidance on model specifications, insights into custom build options, or simply need a few questions answered, our team is ready to assist. With years of experience in yacht building, we’re dedicated to understanding your unique vision and helping you navigate the entire process with ease. Reach out to us by email at info@northpacificyachts.com for personalized responses to all your inquiries.
If you’d prefer a conversation, we invite you to give us a call at 1-877-564-9989. Speaking directly with our experienced team can provide immediate answers and professional insights into everything from specific build features to delivery timelines. At North Pacific Yachts, your satisfaction is our top priority, and we’re here to ensure you’re confident and informed at every step of your yacht ownership journey.